نیتروژندهی پلاسمایی - یونی (Ion Nitriding-Plasma Nitriding)
نیتروژندهی (نیتراسیون)، اشباع سطح قطعه با نیتروژن بهوسیله عملیات ترموشیمیایی است. براثر نفوذ نیتروژن داخل قطعه، نتایج به شرح ذیل بهدست میآید:
– افزایش مقاومت به سایش (سختی بالا)،
– حفظ چقرمگی مغز قطعه،
– افزایش مقاومت به خستگی،
– افزایش مقاومت به خوردگی شیمیایی،
– کمشدن احتمال ایجاد ترک در قطعه.
نیتروژندهی حمام نمک، نیتروژندهی گازی، و نیتروژندهی پلاسمایی انواع مختلف نیتروژندهی هستند.
نیتروژندهی پلاسمایی در یک محفظه خلأ متصل به ولتاژ بالا انجام میشود. در این سیستم، قطعات کاتد، و محفظه خلأ آند میباشد. براثر اعمال ولتاژ، داخل محفظه پلاسما تشکیل میشود. گازهای داخل محفظه (نیتروژن، هیدروژن، و آرگون) یونیزه شده و یونهای آزادشده سطح قطعه را بمباران میکنند که در نتیجه قطعه گرم، سطح آن تمیز، و نیتروژن جذب سطح میشود.
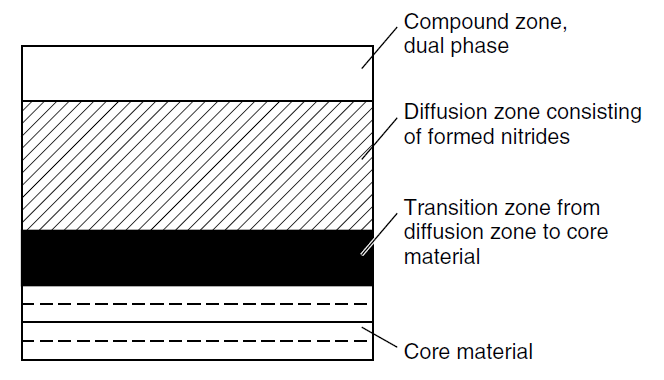
مراحل فرایند نیتروژندهی پلاسمایی
– اسیدشویی و چربیگیری قطعات مطابق دستورالعملهای از پیش تعیینشده؛
– چیدمان قطعات داخل کوره با الزامات از پیش تعیینشده؛
– ایجاد خلأ در کوره تا ۰/۵ میلیبار؛
– اجرای فرایند تمیزکاری به روش کندوپاش (Sputtering) در فشار پایین اتمسفر آرگون و هیدروژن و دمای مشخص؛
– اجرای برنامه نیتروژندهی برحسب نوع قطعات و کارکرد آنها؛
– سردشدن قطعات در خلأ یا گاز خنثی بهمنظور جلوگیری از اکسیدشدن سطح قطعات.
مزیتهای نیتروژندهی پلاسمایی
– امکان نیتروژندهی در دماهای پایین (دمای بالاتر از ۳۷۰ درجه سانتیگراد) و محدوده دمایی گسترده؛
– امکان نیتروژندهی انتخابی (ماسککردن قسمتهایی از قطعه که نباید نیتروژندهی شوند)؛
– امکان تمیزکاری سطحی در داخل محفظه نیتروژندهی؛
– تغییر ابعادی بسیار کم؛
– سختی بالاتر نسبت به روشهای دیگر؛
– امکان نیتروژندهی فولاد زنگنزن بدون نیاز به برداشتن لایه پسیو؛
– اتوماسیون فرایند و تکرارپذیری بالا؛
– کیفیت سطحی مناسب و عدم نیاز به فرایند تکمیلی جهت افزایش کیفیت سطحی؛
– یکنواختی لایه حتی در شکلهای پیچیده؛
– ایجاد لایه سفید چگال، غیرمتخلخل، و با چقرمگی مطلوب؛
– امکان کنترل فاز لایه سفید (گاما پرایم یا اپسیلون) و نیز امکان حذف لایه سفید؛
– مصرف انرژی پایین؛
– عدم آلودگی محیط زیست.
کاربردهای نیتروژندهی پلاسمایی
برخی از کاربردهای نیتروژندهی پلاسمایی به شرح ذیل هستند:
– انواع قطعات اتومبیل: میللنگ، میل بادامک، چرخدنده، و …؛
– انواع قالب: فورجینگ (سرد و گرم)، دایکست، پلاستیک، اکستروژن و …؛
– سیلندر و ماردون تزریق پلاستیک؛
– تجهیزات نورد سرد و گرم؛
– انواع شفت، اسپیندل، و چرخدنده مربوط به صنایع مختلف؛
– تجهیزات حفاری؛
– تجهیزات پزشکی.
نیتروژن-کربندهی پلاسمایی (Plasma Nitrocarburizing)
نیتروژن-کربندهی پلاسمایی مشابه فرایند نیتروژندهی پلاسمایی است؛ با این تفاوت که مقدار کمی از یک گاز حاوی کربن (مانند متان) به اتمسفر کوره اضافه میشود. حضور کربن در اتمسفر کوره باعث افزایش ضخامت لایه سفید میشود. معمولاً فرایند نیتروژن-کربندهی روی فولادهایی استفاده میشود که از نظر عناصر آلیاژی ضعیفاند و امکان تشکیل لایه نفوذی سخت در آنها وجود ندارد. با انجام فرایند نیتروژن-کربندهی در چنین فولادهایی، لایه سفید ضخیم و سخت تشکیل میشود و در نتیجه سختی سطحی قطعه افزایش مییابد.
اکسیداسیون تکمیلی (Post Oxidation)
پس از فرایند نیتروژندهی یا نیتروژن-کربندهی، میتوان فرایند تکمیلی اکسیداسیون را در محفظه انجام داد. هدف فرایند اکسیداسیون تکمیلی تشکیل لایه مگنتیت (Fe3O4) به ضخامت ۲-۳ میکرومتر است. این لایه سیاه است و باعث افزایش مقاومت به خوردگی شیمیایی قطعه میشود.
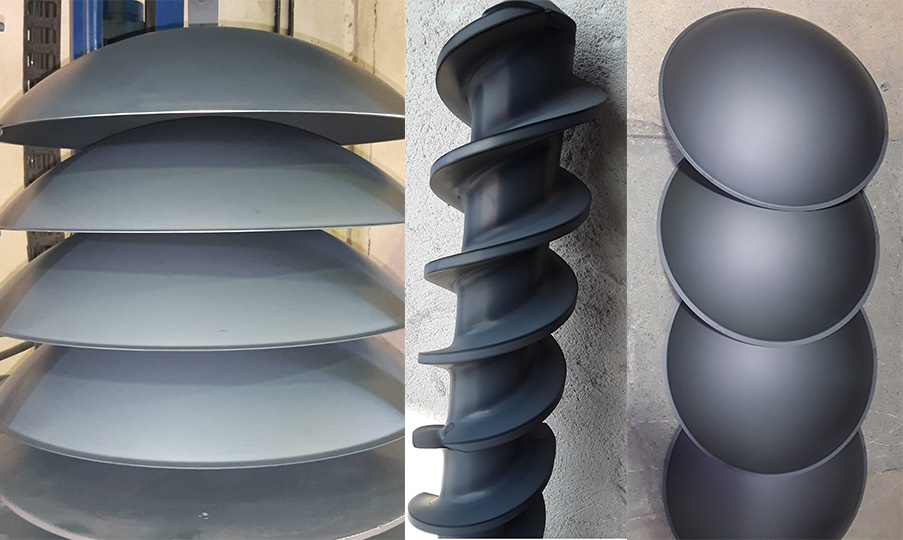
نیتروژندهی تیتانیوم
امروزه، تیتانیوم بهدلیل سبکبودن، استحکام، و مقاومتبهخوردگی کاربردهای بسیاری در صنعت پیدا کرده است، ولی ضعیفبودن مقاومتبهسایش باعث ایجاد محدودیتهایی در استفاده از آن شده است. نیتروژندهی تیتانیوم یکی از روشهای افزایش بهبود خواص سطحی آلیاژهای تیتانیوم است. حین نیتروژندهی، فازهای TiN و Ti2N تشکیل میشوند که باعث افزایش مقاومتبهسایش میشود. نیتروژندهی تیتانیوم بهدلیل نیاز به دمای بالاتر از دمای نیتروژندهی فولاد، مشکل بوده و نیازمند وجود تجهیزات و دانش فنی خاصی است.
کورههای نیتروژندهی شرکت پلاسما پژوه پارس
شرکت پلاسماپژوه پارس در حال حاضر با 6 کوره نیتروژندهی پلاسمایی فعال (در سه کارگاه این شرکت) با ابعاد مختلف که در همین مجموعه ساخته شدهاند، در حال ارائه خدمات در زمینههای زیر است:
– نیتروژندهی فولاد، چدن، و تیتانیوم
– نیتروژن-کربندهی فولاد
– اکسیداسیون تکمیلی فولاد
وجود چند کوره با ابعاد مختلف در مجموعه دو مزیت زیر را ایجاد کرده است:
– سرعت انجام خدمات در مجموعه بالاست و معمولاً مشتریان شرکت زمان انتظار کمی را سپری میکنند.
– در صورت وجود یک کوره در مجموعه، تمام قطعات باید با یک سیکل عملیات شوند؛ اما باوجود چند کوره در مجموعه، امکان انجام فرایند با پارامترهای مشخصشده بر اساس هر قطعه، برحسب نوع آلیاژ، عملکرد، و ابعاد وجود دارد.
در حال حاضر، امکان انجام فرایند روی قطعاتی با قطر حداکثر 180 سانتیمتر، ارتفاع حداکثر 280 سانتیمتر، و وزن حداکثر 10 تن در مجموعه وجود دارد.