Plasma (ionic) nitriding
Nitriding is the saturation of the surface of a component with nitrogen by thermochemical operations. Due to the penetration of nitrogen into the component, the results are obtained as follows:
Increased abrasion resistance (high hardness)
Maintain the toughness of the base metal,
Increased fatigue resistance,
Increase chemical corrosion resistance,
Reduces the possibility of cracks in the piece.
Salt bath nitriding, gas nitriding, and plasma nitriding are different types of nitriding.
Plasma nitriding takes place in a vacuum chamber connected to a high voltage. In this system, there are cathode components and an anode vacuum chamber. by the application of voltage, the plasma is formed inside chamber. The gases inside the chamber (nitrogen, hydrogen, and argon) ionize, and the released ions bombard the surface of the part, so the part bacome warm, its surface clean, and nitrogen adsorp on the surface.
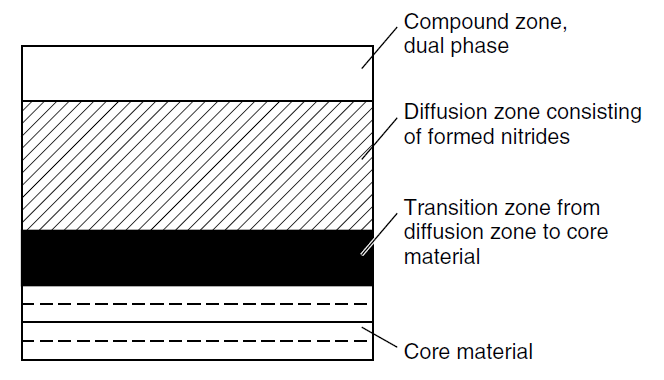
Plasma nitriding process steps
Acidwashing and degreasing of parts according to pre-determined instructions;
Arrangement of parts inside the furnace with predetermined requirements;
Creating a vacuum in the furnace up to 0.5 millibars;
Execution of sputtering cleaning process at low pressure of argon and hydrogen atmosphere and specific temperature;
Implementation of nitriding program according to the type of components and their function;
Cool the parts in vacuum or neutral gas to prevent the surface of the parts from oxidizing.
Advantages of plasma nitriding
Possibility of nitriding at low temperatures (temperatures above 370 °C) and wide temperature range;
Possibility of selective nitriding (masking parts of the part that should not be nitrogenized)
Possibility of surface cleaning inside the nitrogenation chamber;
Very small dimensional change;
Higher hardness than other methods;
Possibility of nitrogenation of stainless steel without the need to remove the passive layer;
Process automation and high repeatability;
Appropriate surface quality and no need for a complementary process to increase surface quality;
Layer uniformity even in complex shapes;
Creating a dense, non-porous, white layer with the desired toughness;
Ability to control the white layer phase (gamma prime or epsilon) and also the possibility of removing the white layer;
Low energy consumption;
No environmental pollution
Applications of plasma nitriding
Some of the applications of plasma nitriding are as follows:
Types of car parts: crankshafts, camshafts, gears, etc .;
Types of molds: forging (hot and cold), die-casting, plastic, extrusion, etc .;
Cylinder and Mardon plastic injection;
Hot and cold rolling equipment;
Types of shafts, spindles, and gears related to different industries;
Drilling equipment;
Medical equipment.
Plasma Nitrocarburizing
Plasma nitrogen-carbonation is similar to the plasma nitrogenation process; The difference is that a small amount of a carbon-containing gas (such as methane) is added to the furnace atmosphere. The presence of carbon in the furnace atmosphere increases the thickness of the white layer. The nitrogen-carbonation process is usually used on steels that are weak in terms of alloying elements and do not have the possibility of forming a hard penetration layer. By performing the nitrogen-carbonation process in such steels, a thick and hard white layer is formed, resulting in an increase in the surface hardness of the part.
Post Oxidation
After the nitrogenation or nitrogen-carbonation process, a supplementary oxidation process can be performed in the chamber. The goal of the complementary oxidation process is to form a 2-3 μm thick magnetite layer (Fe3O4). This layer is black and increases the chemical corrosion resistance of the part.
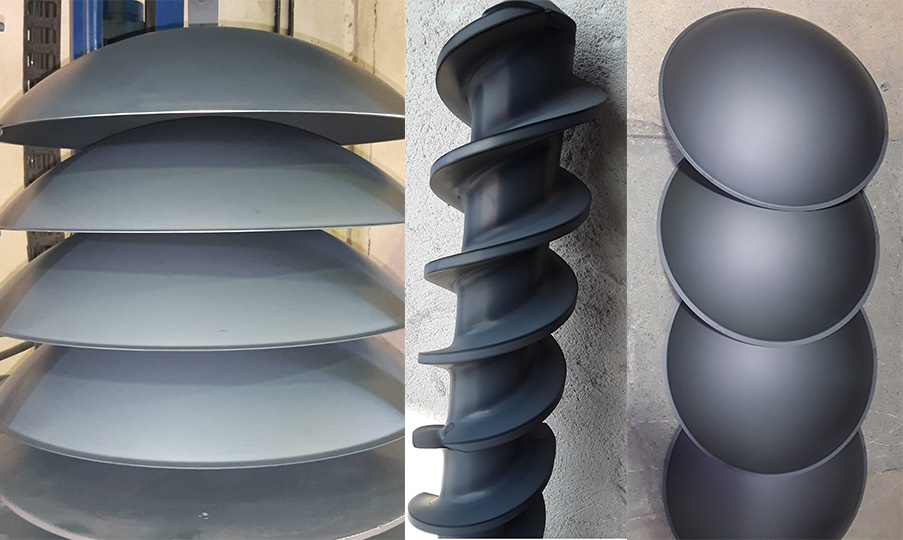
Titanium nitrogenation
Today, titanium has found many applications in industry due to its lightness, strength, and corrosion resistance, but weak wear resistance has led to limitations in its use. Titanium nitrogenation is one of the methods to increase the improvement of surface properties of titanium alloys. During nitrogenation, TiN and Ti2N phases are formed, which increases the wear resistance. Titanium nitrogenation is difficult due to the need for temperatures higher than the nitrogenation temperature of steel and requires special equipment and technical knowledge.
Nitriding furnaces of Plasmapazouh Pars Company
Plasmapazhouh Pars Company is providing services in the following fields by 4 plasma nitrogen furnaces with different dimensions that have been built in the same complex:
Nitrogenation of steel, cast iron, and titanium
Nitrogen-carbonation of steel
Complementary oxidation of steel
The existence of several furnaces with different dimensions in the set has created the following two advantages:
The speed of service delivery in the complex is high and usually the company’s customers spend a little waiting time.
If there is a furnace in the set, all parts must be operated in one cycle; However, despite the fact that there are several furnaces in the complex, it is possible to perform the process with the specified parameters based on each part, depending on the type of alloy, performance, and dimensions.
At present, it is possible to perform the process on parts with a maximum diameter of 90 cm, a maximum height of 280 cm, and a maximum weight of 4 tons in the set.